Those old ceramic tiled floors that were installed during the days of the Roman Empire are still beautiful today. We admire them and yet most have a crack through them that we accept and say the crack adds character to the floor. Today, we do not expect to see any cracks in contemporary ceramic or natural stone tiled floors. If a crack appears in one of these floors, the owner immediately requests that the tiles be replaced.
:max_bytes(150000):strip_icc()/fortifiber-underlayment-70-195-64_1000-40c82d9654004fc7ab641206f6b7dbf1.jpg)
In 2005, ANSI published a standard for Crack Isolation Membrane, A118.12. This gave the products credibility and their use by installers became common place in tile assemblies. Crack isolation membranes provide the lowest profile (elevation or thickness) of the tile or stone tile installation incorporating a crack isolation membrane. A118.12 was developed to provide a standard with the minimum criteria necessary for a material to function as a deterrent to crack propagation from the substrate through the finished thin. 170.5 Sound & Crack Isolation Mat is a high performance anti-fracture / sound and crack isolation membrane designed to be used under thin-bed adhesive for interior floor installations of ceramic tile, marble, stone and brick to reduce the transmission of impact noise and help provide soundproofing between floors and isolate cracks in the substrate. Crack isolation membranes provide the lowest profile (elevation or thickness) of the tile or stone tile installation incorporating a crack isolation membrane. A118.12 was developed to provide a standard with the minimum criteria necessary for a material to function as a deterrent to crack propagation from the substrate through the finished thin. PROFLEX AF300 (Anti-Fracture 300) is a ready-to-use single component mold resistant crack-isolation membrane. AF300 provides a uniform surface with excellent elongation to prevent in-plane cracks up to 3/8” from the substrate to the finished ceramic, porcelain, or stone tile.
:max_bytes(150000):strip_icc()/quietwalk-underlayment-qw100b1lt-64_1000-ecc5026e845c4bd3a6d66c4118795b98.jpg)
Traditionally the way to prevent cracks in the ceramic tile was to install them on an unbonded reinforced mortar bed. The installer would construct a 1 ½” reinforced cement mortar bed over a cleavage membrane that was laid on the concrete substrate. Since the cleavage membrane was not bonded to the concrete below it, movement in the concrete slab was not transmitted to the tile above. The ceramic tile was isolated from any cracks that would develop in the concrete below; as we know it is only matter of time before that concrete will crack. To accommodate for a tile installation, generally, the concrete slab is depressed a couple of inches, when the it is poured; this allows room for the thick mortar bed. Unfortunately, this is not always the case today and often the installer does not have the necessary elevation to install the proper unbonded reinforced mortar bed. Fortunately today we have many options to help isolate ceramic tile from the movement of the concrete slab below it.
So why does a concrete slab crack and can it be prevented? As concrete cures, it shrinks and because of its size and mass it does not just get smaller, it cracks at the weakest point. Shrinkage reducers can be added to the concrete mix and this will minimize the cracks, but does not eliminate them. Typically the concrete is grooved when it is finished or saw cuts are made shortly after it is placed to control where the crack will be. This eliminates the random cracks in the concrete slab and helps in the placement of floor coverings and movement joints. It is beneficial to know where the crack is so that measures can be made to isolate them from ceramic tile installed over these soon to be cracks in the floor.
:max_bytes(150000):strip_icc()/QEP200sq.ft.14in.CorkUnderlaymentRoll-5a3415b0e258f80036a17626.jpg)
It is more important today to protect the tile from cracks than it has ever been. In the early 1950’s, new tile manufacturing processes and simplified installation products made it more affordable to install ceramic tile. At this time there was an expansion of porcelain tile availability and the dimensions of tile grew as the market quickly increased. As tile got physically larger, it became more important to protect the tile from cracks that occur in the concrete substrate. Crack isolation membranes appeared on the market as a low profile way to protect the ceramic tile and gained popularity quickly amongst installers. The early products were sheet applied from rolls of elastomeric materials. Later in the 1980’s we began to see liquid applied, elastomeric membranes that could be installed over the crack in the slab to stop it from cracking the tile above. In 2005, ANSI published a standard for Crack Isolation Membrane, A118.12. This gave the products credibility and their use by installers became common place in tile assemblies. Today nearly every ceramic tile installation over concrete includes a crack isolation membrane. But, how do you know when the membrane is necessary and what product do you use.
Nearly all the details in the Tile Council of North America (TCNA) Handbook show that a crack isolation membrane is optional. Detail F125 shows the installation of a crack isolation membrane over an existing crack, and offers either full or partial coverage of the crack and relocation of a soft joint in the tile; which is it, partial or full coverage. As we all know, there is concrete floors with cracks and floors that someday will have cracks. Once cracked, the concrete does not stop moving, as temperature and humidity fluctuates the concrete will expand and contract; the crack will open and close. It is important to protect the expensive ceramic and natural stone tile from what is going on below. The rule is that the membrane over a crack should extend out the diagonal width of the tile on either side of the crack. The membrane width should be at least two times the diagonal width of the tile. This assures that the tile straddling the crack is bonded to the membrane alone and not the concrete on both sides of the crack. If you are installing a large format 36 inch tile, the membrane should be 9 feet wide. If you have more than one crack in the floor, in many cases you have nearly covered the entire floor; so why not just install full coverage membrane. Remember, it is the responsibility of the Architect or Owner to specify full membrane coverage, the installer should not make this decision. TCNA requires that a crack isolation membrane be installed on above ground concrete floors when an ANSI A118.4 thin set mortar is used to install large format tile. Crack isolation membranes may be optional in the TCNA Handbook, but where would you not install it to protect the tile is the real question. With the vast array of crack isolation membranes available, how does one choose the right one for their job.
First it is important that the membranes meets the requirements of ANSI A118.12. Since many manufacturers self certify to that standard, confirm the manufacturer’s reputation and that they back their claims with an inclusive warranty. Next is the decision between liquid and sheet applied. Both have their pros and cons.
Crack Isolation Membrane Home Depot Tiles
For the most part liquid applied is easier to install, you just roll, brush, trowel or spray it on the floor. It is critical to apply the right thickness, for the membrane to function as required. If you are covering 2000 square feet and the membrane instructions state that one gallon covers 100 square feet, you must use 20 gallons for proper coverage. Alternately, you can check the wet film thickness of the membrane as you progress; just be sure to regularly check the thickness to assure a uniform coating. Liquid applied has no seams to worry about and it is easy to go around obstacles in the floor. The downside of using a liquid applied is you have to wait for them to dry. So if your timeline is tight, this may not be the best choice.
Ceramic tile can be installed immediately on sheet applied membranes. Once the membrane is adhered to the floor, it is ready to accept the installation of ceramic tile with a thin set mortar. However, it is much more complicated installing sheet applied membrane. The sheet must be cut and bonded to the floor. In some cases this means spreading a mortar or adhesive on the floor and placing the membrane while it is wet. Some membranes have a peel and stick adhesive, ready to be stuck to the floor, except they require a primer applied first to the floor and allowed to dry. Keeping the seams tight as you roll out 100 feet of peel and stick membrane can be a challenge, but it is important to keep the seams closed. Once it is in place it is ready to tile.
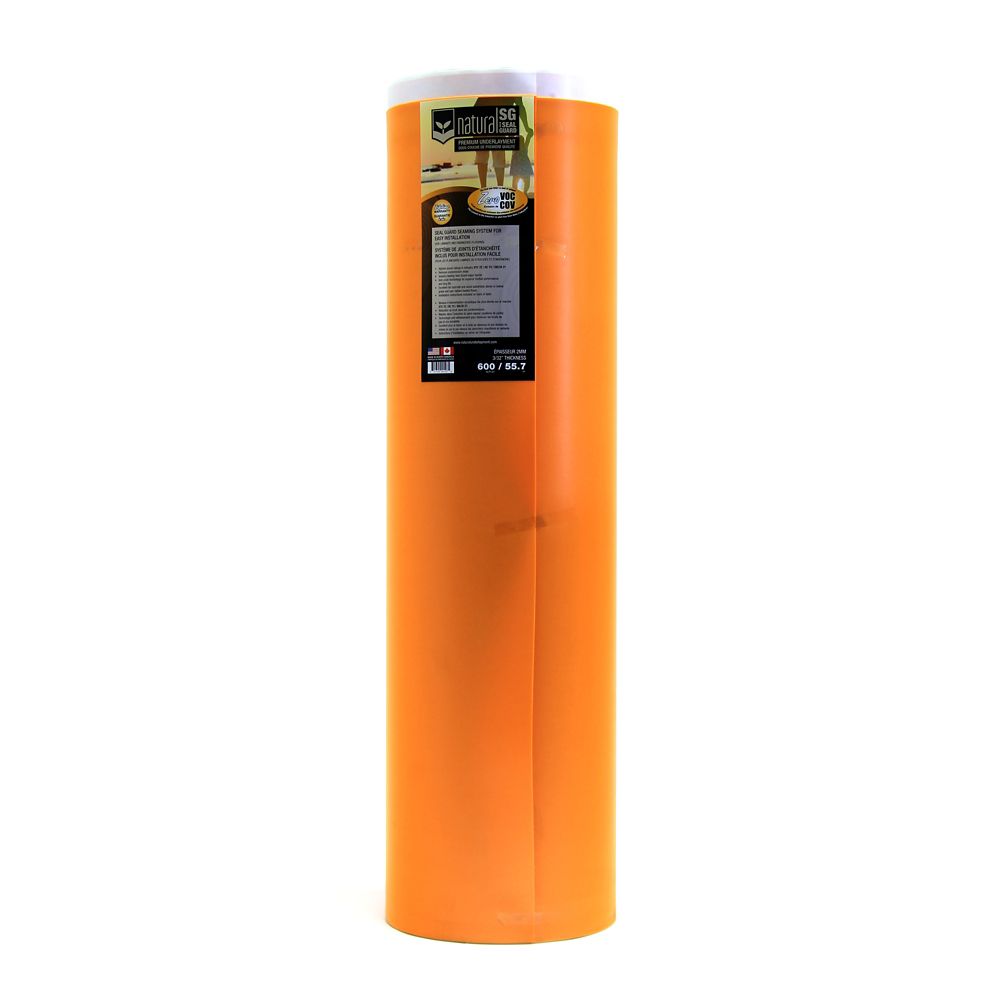
Uncoupling membranes are a special class of sheet applied crack isolation membranes. The true advantage of using one of these membranes is that they can be installed on “young” concrete. “Young” concrete is defined as the earliest that the builder says it is safe to walk on; this can be as little as a few days. The uncoupling membrane will help divert moisture from the concrete and aid in curing. The plastic uncoupling membrane will deform under stress and absorb slab movement that would normally crack a tile.
Now that you have a plan that will assure that the tile will not crack when properly installed, it is important to follow all industry guidelines including the placement of movement joints in the tile assembly. The TCNA Handbook gives proven guidelines for installing movement joints in EJ171. Following these guidelines will allow the tile and concrete to move independently to environmental changes.
Crack Isolation Membrane Home Depot Insulation
So much effort has been put into preventing damage to the tile. Make sure the assembly last a lifetime with high performance thin set mortar and grout from a prominent manufacturer. It is much easier to do it right the first time, than coming back to fix the floor at your cost.
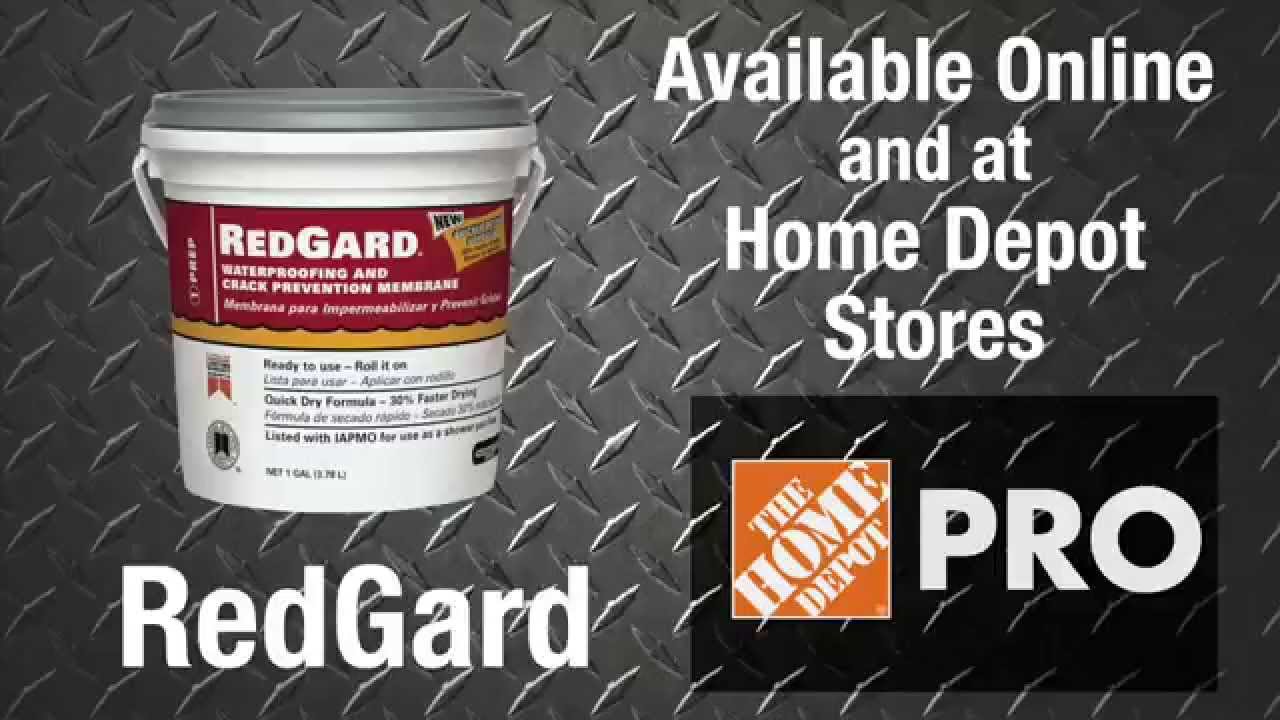
Two thousand years from now people will look at the tiled floors from the early 2000’s and appreciate their beauty, without the cracks.
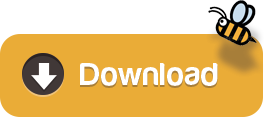